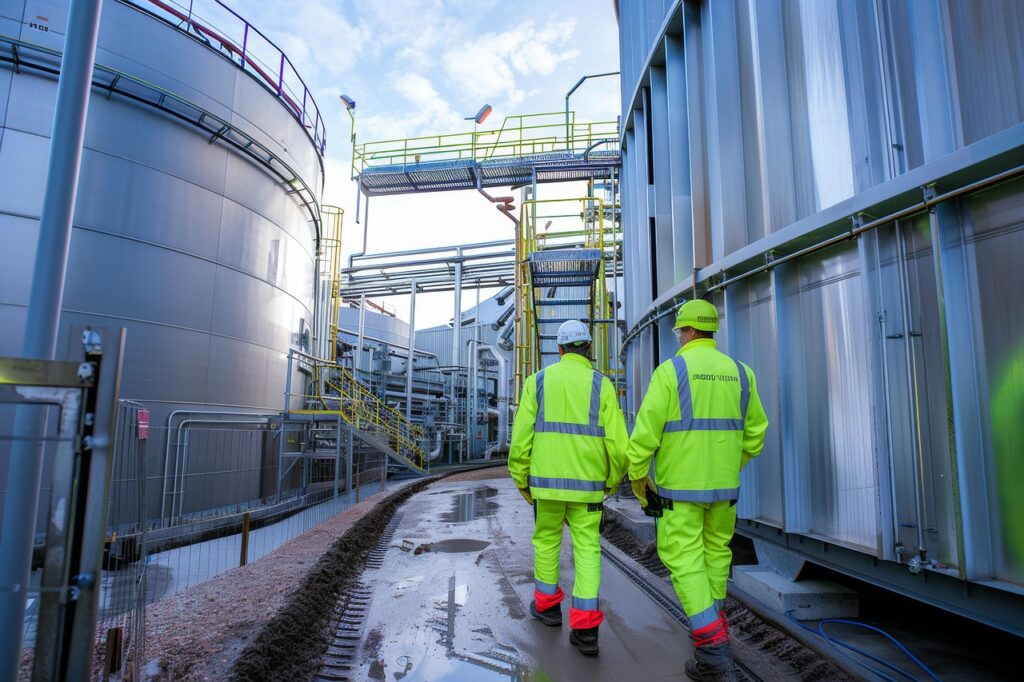
The ground is shifting beneath manufacturing leaders. Disruption isn’t occasional—it’s constant. McKinsey’s 2024 supply chain survey reports that, nine in ten respondents say they have encountered supply chain challenges in 2024. By 2033, the industry will need to fill 3.8 million new roles, yet nearly half of these positions may go unfilled due to widening skills gaps.
These challenges also extend to on-site safety concerns. Injuries and equipment failures can lead to significant disruptions, including unplanned downtime, production delays, and ballooning costs. According to the U.S. Bureau of Labor Statistics, the manufacturing industry witnessed 391 fatal occupational injuries in 2023.
The stakes for effective manufacturing risk assessments have never been higher. Yet, most manufacturers are still managing risk with outdated, static processes, often reviewing safety and operational risks only once or twice a year. If your risk management feels reactive, slow, or fragmented, you’re not alone, but saving that action for next quarter is no longer an option.
Here are seven reasons why many manufacturers are still relying on outdated risk assessments, and why now, more than ever, is the time to invest in your manufacturing safety programs.
1. Inefficient, Manual Processes Are Slowing You Down
Despite advances in technology, many manufacturers still manage risk using spreadsheets, emails, and ad hoc phone calls. This patchwork approach leads to fragmented data, delays in response time, and missed insights. Manual systems can’t keep pace with the velocity of risk in today’s environment, especially when unplanned downtime already costs manufacturers an estimated $50 billion per year.
2. Data Lives in Silos—And It’s Not in Real Time
When you operate across multiple plants, departments, or countries, risk data often becomes siloed. Without a centralized system that delivers real-time visibility, risk leaders are left cobbling together information-often after it’s too late to act effectively.
3. Teams Aren’t Talking—and Risks Are Falling Through the Cracks
Risk doesn’t respect department lines. When EHS, operations, quality, and executive teams fail to collaborate, critical areas get overlooked. Lack of cross-functional communication means one team may be solving yesterday’s problems while another is unaware of tomorrow’s threats.
4. Risk Assessments Are Infrequent and Quickly Outdated
Conducting an annual manufacturing risk assessment might meet compliance requirements, but it won’t prepare you for the pace of change today. Risks evolve in real time, and assessments need to evolve with them. Relying on a once-a-year snapshot leaves your business exposed for the remaining 11 months. Consider quarterly or even monthly manufacturing risk assessments to stay on top of evolving conditions.
5. Your Technology Is Holding You Back
Spreadsheets aren’t built for risk intelligence. Legacy tools lack automation, audit trails, and actionable insights. Without modern platforms to aggregate, analyze, and flag critical risks, even experienced teams can miss what matters most.
6. The Focus Is Compliance—Not Prevention
Too often, risk management is treated as a checkbox exercise. If your approach is designed primarily to pass audits or respond to incidents, you’re missing the bigger opportunity: preventing them in the first place.
7. There’s No Standard—and That’s a Risk in Itself
When each site or team uses its own methodology to assess risk, it becomes impossible to see the big picture. Inconsistent scoring systems, templates, and reporting structures prevent you from prioritizing effectively or comparing risk across locations.
Ready to Modernize Your Risk Strategy?
Outdated manufacturing risk assessments won’t keep your teams safe—or your operations running. YellowBird connects you with certified EHS professionals who conduct fast, thorough, and actionable safety assessments tailored to your facilities, risks, and industry needs, when you need them.
Whether you’re managing one site or 100, YellowBird helps you:
- •Identify critical, unseen areas that pose risk to your people and your operations
- •Standardize risk evaluation across locations
- •Move from reactive to proactive with real-world recommendations