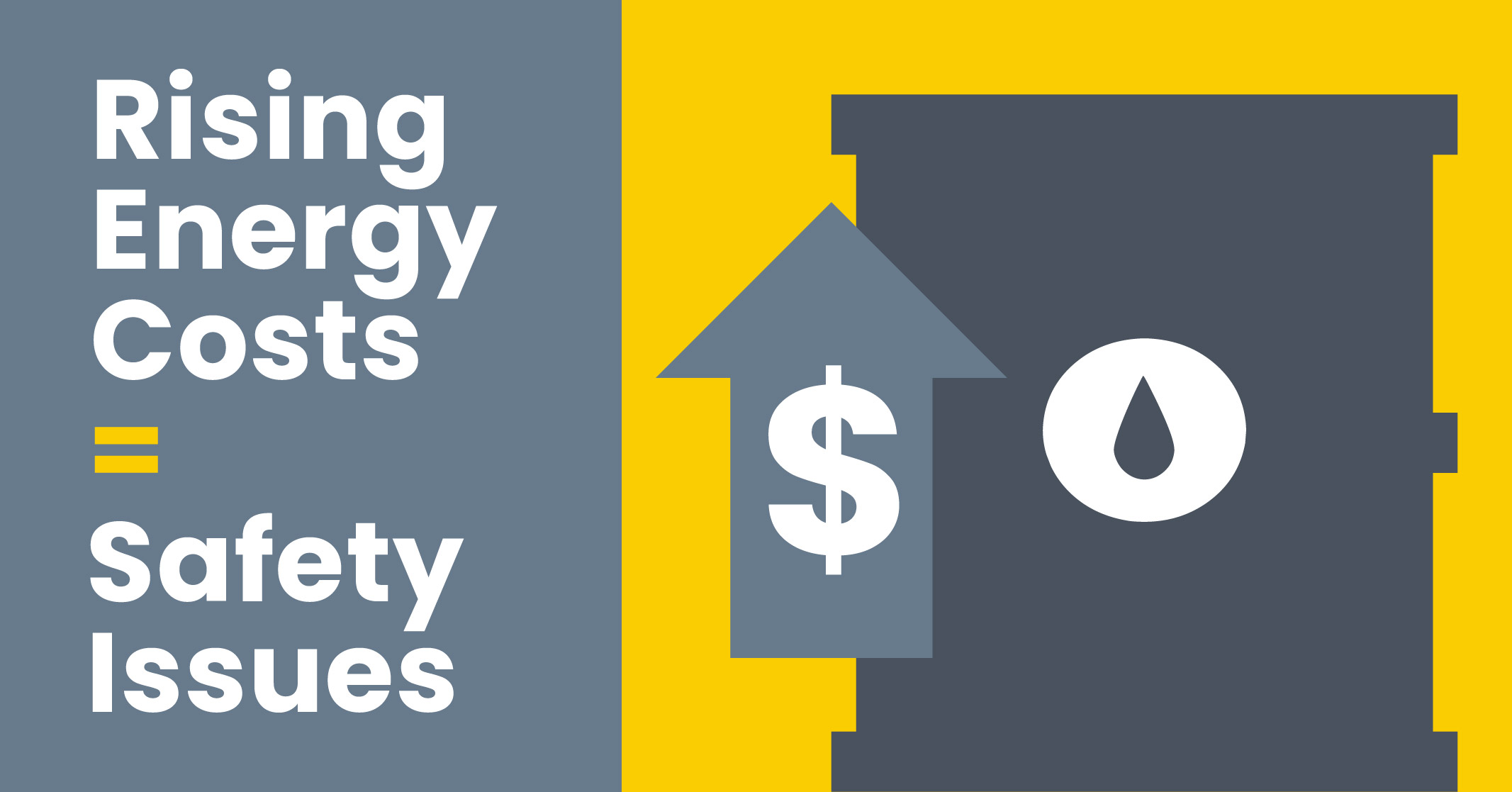
How Energy Prices Are Creating Industrial Manufacturing Safety Concerns
In their recent report, “Driving Toward Disaster,” the Consumer Energy Alliance (CEA) projected that the rising cost of electricity, natural gas, and diesel fuel to industrial manufacturing companies in 2022 would be 41.4 billion USD higher than in 2021. Their findings were based on the U.S. Energy Information Administration’s (EIA) Short Term Energy Outlook. These findings point to a reality that environmental health and safety (EHS) companies experience each day: Energy prices are on the rise, and they’re hurting the bottom line.
To improve profitability without damaging productivity, some industrial manufacturing companies are taking steps to use their energy resources more efficiently. Many of these steps comply with regulatory standards and can even improve working conditions, but others can endanger employee health. And even if a cost-cutting strategy can be safely implemented, doing so can prove a logistical challenge at best. By heeding the recommendations of an EHS professional, companies can curb their energy bill while keeping their workforce safe.
Sourcing Unsafe Energy
A host of factors have made securing reliable, efficient energy resources a difficult task in 2022. An ongoing pandemic, military conflicts, and supply chain strains have forced the industrial manufacturing sector to explore new energy alternatives — but these may be unreliable and even harmful to the environment. For example, a company that finds its utility costs rising may turn to natural gas as a way to heat or power its facilities. However, without the proper filtration technology, pollutants like SOx and NOx can be emitted, causing further damage to the atmosphere.
Switching to a potentially unreliable energy source may not have only environmental consequences. The health of employees and surrounding citizens could be impacted, as well. For instance, in 2020, a gas leak at a chemical factory in India resulted in the emission of noxious fumes into a neighborhood nearby, killing 11 people and hospitalizing many more. A catastrophic ignition in the event of a spark or mishandling is another potential risk, and many others show that the cost of switching to an unreliable or potentially unsafe alternative vastly outweighs the benefit of mitigating utility costs.
Organizational Chaos of Changing Energy Sources
Industrial manufacturing companies are right to explore the many viable energy alternatives. Some energy alternatives can reduce carbon emissions, improve efficiency, bolster productivity, and either have a neutral or positive impact on employee health — if they’re implemented correctly.
Pivoting to new energy infrastructure is a daunting task, and the transition comes with a host of logistical challenges. Design, material sourcing, construction, training, and maintenance are just a few parameters to be accounted for when switching to a new energy source. The challenge is made even more difficult under a tight deadline.
As an example, consider a manufacturer wishing to transition to solar photovoltaics (PV) to meet its energy needs:
- Design: Before a company can begin the installation, they will need to consult an expert to assess their power requirements, location for a PV array, cost of installation, possible use of solar tracking software to elevate power output, and other variables specific to their application. Unique challenges exist for each energy source, but the common denominator is that design takes time.
- Material sourcing: The supply chain is in dire straits, and securing reliable energy sources is difficult across the board. The Department of Energy (DOE) has laid out a framework of case-specific hurdles and opportunities for developing a resilient clean energy supply chain, but the long-term solutions needed for such a system don’t get energy sources to manufacturers right now.
- Construction: Whether they choose a rooftop system or solar farm installation on property nearby, installing a solar PV array isn’t done overnight — and the greater the power requirements, the larger the system and the longer the timeline will be.
- Maintenance: Periodic output checks, cleaning to ensure optimum performance, and protection from environmental damage are a few maintenance requirements associated with PV installations, all of which carry additional time, training, and expense.
- Reliability: Like many energy sources, PV may not produce adequate power under certain environmental conditions. Resulting in a need for power storage sources to be added as a backup, creating one more layer of complexity.
Taken together, the logistical challenges of pivoting to a new energy source under a tight deadline can overwhelm some businesses. The result can be a rushed transfer and costly mistakes that further damage the bottom line.
Negligence Costs More
The potential risks and difficulty of switching to a different energy source may cause some industrial manufacturing companies to reject EHS best practices or not hire an EHS professional at all. The thinking could be that following the recommendations made by EHS professionals would cost too much up front and that greater savings are available by practicing sub-optimal procedures or doing nothing at all. This approach is incorrect.
Some EHS recommendations will indeed require greater funding to fulfill, but these investments are designed to improve workplace wellness — and they’re far less expensive than a violation or hazard. The health risks incurred by poorly transitioning to a new energy source can result in environmental fines, lawsuits, negative publicity, facility downtime, and many other expenses that could have been prevented if an EHS professional had been consulted and their advice had been followed the first time.
An EHS Professional Protects the Bottom Line
Rising energy prices have raised the cost of doing business at a time when inflation has already hindered profitability. As a result, companies need to find reliable, environmentally friendly energy alternatives that both meet their industrial requirements and cut their power costs — but it has to be done right. Hiring an EHS professional can help companies implement new energy solutions that meet their industry needs while improving the health and safety of their workforce at the same time. It’s not just an expense. It’s an investment.
If you’re ready to improve your energy costs while benefiting the health of your workforce, contact Yellowbird today.