What Your Incident Reports Are Secretly Saying About Your Safety Leadership
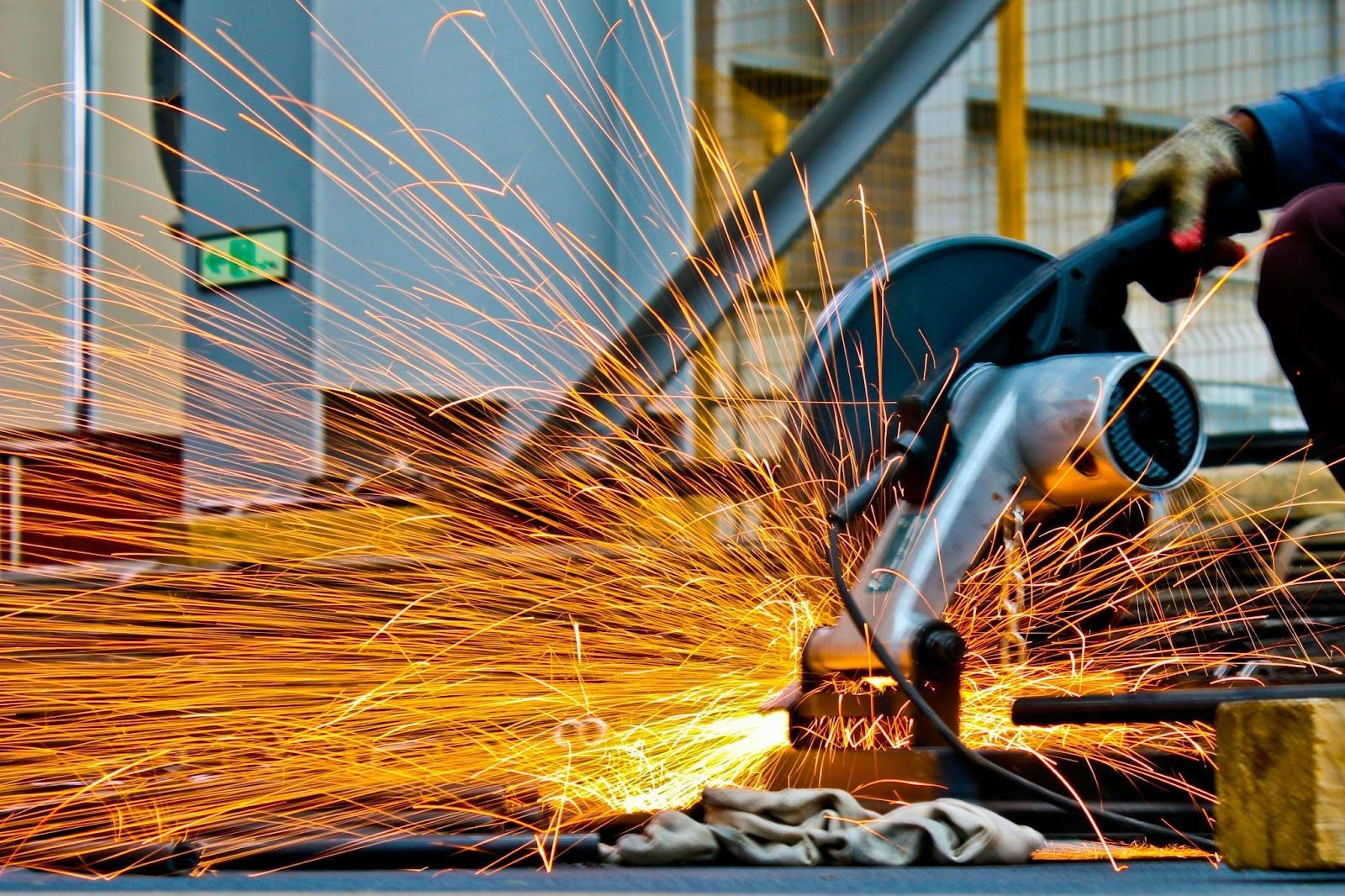
Many safety leaders in construction and manufacturing see incident reporting as necessary but tedious paperwork. But behind every slip, near miss, and equipment failure is a story—about your safety leadership style.
Your safety logs don’t just catalog what went wrong; they reveal how your team operates when you’re not looking. They speak volumes about your leadership style, your company’s safety culture, and—perhaps most importantly—what your team really thinks about your priorities.
Why Incident Reporting Reflects Safety Leadership
Incident reporting isn’t just about cataloging what went wrong. It’s a direct reflection of your safety leadership strategies and how your team operates when you’re not present. These reports reveal the true safety culture within your organization and what your workforce really believes about your priorities.
Repeating Incidents Signal Leadership Gaps
If the same types of incidents—slips, trips, equipment misuse, overlooked PPE—keep cropping up in your reports, it’s not just a safety concern. It’s a communication breakdown.
In 2023, U.S. construction saw 1,008 worker deaths—21% of all workplace fatalities—with falls, struck-by incidents, and equipment failures leading the pack. In manufacturing, overexertion and being struck by objects are top injury causes, and 35% of injuries happen to first-year employees.
If you’ve already tried training, reminders, or new signage with no change, your team may have tuned out. When workers stop responding to prevention strategies, it signals they no longer believe leadership is serious about safety—or that your messaging simply isn’t getting through.
Takeaway: Repetition = Resistance = Leadership Gap. Addressing these patterns is critical for effective safety leadership in construction and manufacturing.
Near Misses: A Window into Safety Culture
A high volume of near-miss reports often means your people trust the system enough to speak up. But if your logs are too clean, ask yourself: are people afraid to report? Have they seen previous warnings ignored? Are they too burned out to bother?
In high-risk industries, observation reporting is essential—studies show that implementing behavior-based safety measures can reduce injuries by 25% in the first year.
Takeaway: The absence of near misses doesn’t necessarily mean people are safer. It might mean there’s a lack of communication.
The Tone of Incident Reports Reveals Culture
Are incident descriptions detailed and solution-oriented, or vague? The tone of your reports tells you if your people are engaged—or just checking a box. If your reports feel like CYA documents rather than safety insights, that’s not a workforce issue. That’s a signal to leadership.
Takeaway: How your team writes tells you how they think, and how they think reflects the culture you’ve created.
Your Reactions Speak Louder Than Your Policies
Every leader has a default reaction to bad news. Some panic. Some discipline. Some fix.
Your team watches how you respond more than what you say. If incident reports are met with finger-pointing or shame, don’t be surprised when employees speak out less. But if your reaction is calm, curious, and constructive, you reinforce a culture where learning is valued over blame.
Takeaway: Every reaction is a signal—and a training moment. Your leadership shows up most clearly in moments of crisis.
Real-World Stats: The Impact of Safety Leadership
- • Only 36% of construction firms involve their safety and health director in pre-task planning, yet those who do report higher worker engagement, fewer injuries, and more predictable costs.
- • 51% of contractors offer mentoring programs, but many lack the training needed to make them effective, especially as the workforce ages and new hires flood in.
- • In manufacturing, the average injury leads to 67 missed workdays, and high turnover (28.6%) is often linked to poor safety culture and leadership gaps.
- • Companies like Alcoa and DuPont saw dramatic improvements in both safety and profitability when leadership made safety a core value—starting every meeting with safety discussions and empowering employees to report hazards directly to top management.
Turn Incident Reports into Leadership Wins
So what do you do with these insights? Turn those reports into action:
- • Spot patterns: Go beyond the obvious. Look for themes in locations, departments, shifts, or even attitudes.
- • Host debriefs: Treat incidents as learning moments—not just for the people involved, but for the whole team.
- • Reward honesty: Celebrate those who flag near misses or report early warnings.
- • Track improvements visibly: Show your team that reporting leads to change, not bureaucracy.
Incident reports aren’t a record of failure. They serve to point out opportunities for improvement.
Takeaway: Leadership isn’t what you say in meetings—it’s what shows up in your reports.
Want to Know What Your Incident Reports Are Really Saying?
YellowBird can help you build a safer, smarter workforce—with expert-led safety training, assessments, policy development, and staffing solutions tailored to construction and manufacturing environments. Gain access to a network of 6,500 pros who are vetted, insured, and ready to work. Many pros who specialize in construction and manufacturing safety can be on your job site or at your facility in as little as 24 hours.