Vital Role of Machine Safety & Operator Training in Manufacturing
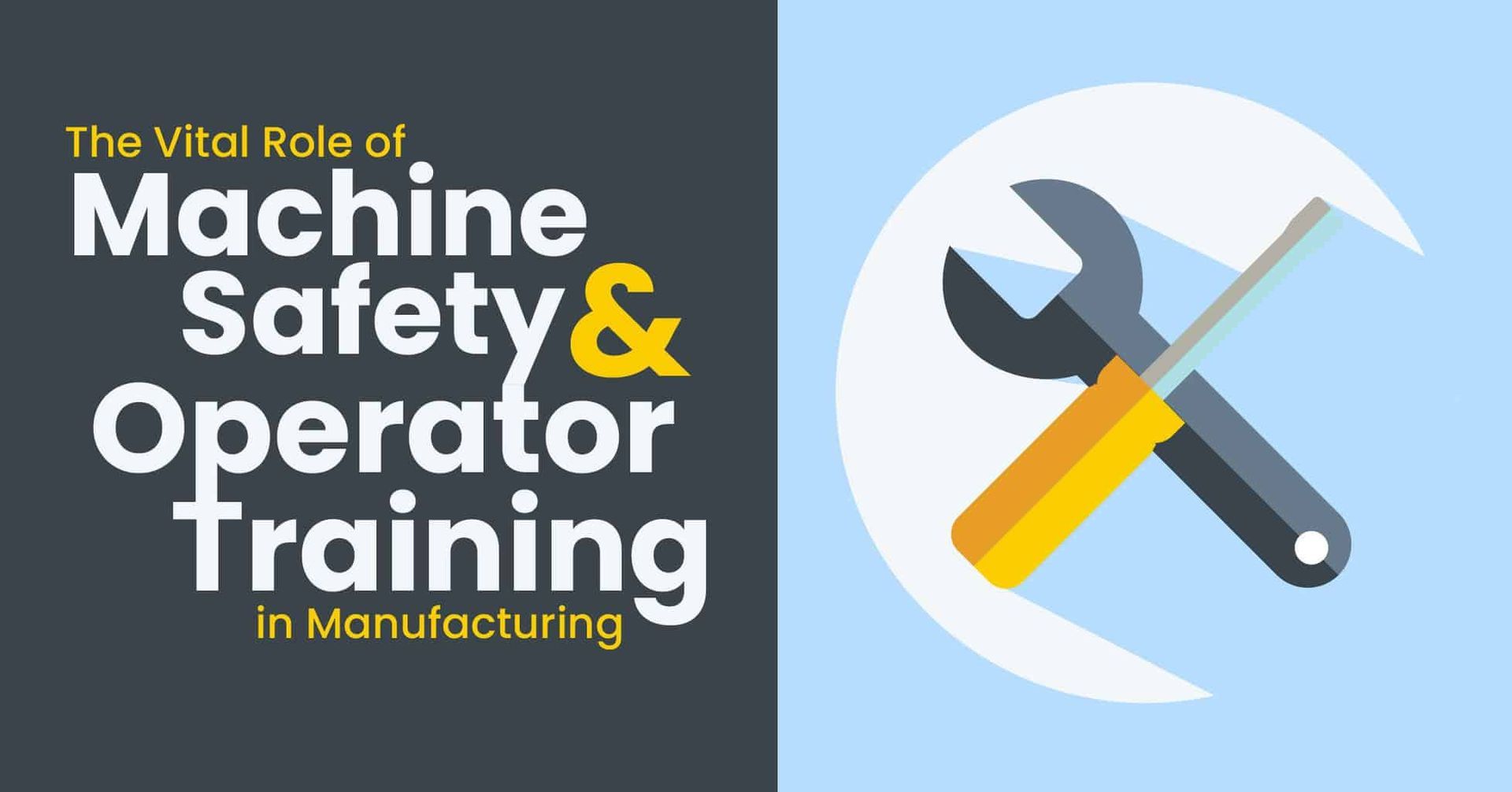
The Vital Role of Machine Safety and Operator Training in Manufacturing
In the bustling world of manufacturing, where precision meets productivity, the safety of both machines and operators is paramount. The manufacturing industry is a complex and dynamic environment where a wide array of machinery, tools, and processes converge. Ensuring the well-being of workers and the integrity of production processes hinges on the meticulous implementation of machine safety protocols and comprehensive operator training. In this article, we will delve into the importance of proper machine safety, including topics such as machine guarding and lockout/tagout procedures, and emphasize the significance of comprehensive operator training to prevent accidents.
The High Stakes of Manufacturing Safety
Manufacturing is a cornerstone of our global economy, providing us with countless goods we use every day. However, the nature of manufacturing also poses significant risks. Data from the U.S. Bureau of Labor Statistics reveals that manufacturing has one of the highest rates of workplace injuries and fatalities among all industries. * These statistics underscore the need for robust safety measures.
1. Machine Guarding: The First Line of Defense
Machine guarding is a primary safeguard in the manufacturing industry. It involves creating physical barriers or shields around machinery to prevent operators from contacting moving parts or hazardous processes. For over the past decade, lack of machine guarding has been on OSHAs yearly “Top 10 Violations” list.**
Machine guarding plays a pivotal role in accident prevention. A well-designed guard can prevent recordables such as:
- Crush Injuries: Guards can protect operators from getting caught in or between machine parts, which can lead to devastating crush injuries.
- Lacerations: Rotating gears, blades, or other machinery components can cause severe lacerations. Guards provide a barrier against such incidents.
- Amputations: Without proper guarding, machines with exposed moving parts pose a substantial risk of amputation.
Implementing and maintaining machine guarding is not just a regulatory requirement; it is a moral obligation to protect the lives of the workforce.
2. Lockout/Tagout Procedures: Safeguarding Against Unintended Activation
Machines often need maintenance or repairs, which means that workers may need to interact with them even when they are not actively in production. This is where lockout/tagout (LOTO) procedures become crucial. LOTO is a set of safety protocols that ensure machinery is safely powered down and locked out before any maintenance or servicing occurs.
Recent research from the National Safety Council (NSC) indicates that nearly 3 million workers are at risk of lockout/tagout accidents each year.*** Failure to follow these procedures can lead to unintended machine activation, causing severe injuries or fatalities.
The key components of LOTO procedures include:
- Identification: Clearly identifying energy sources, such as electrical, hydraulic, or pneumatic, that need to be controlled during maintenance.
- Locking: Using locks or other devices to secure energy sources, ensuring machines cannot be powered on accidentally.
- Tagging: Attaching warning tags to locked-out machines to inform workers of the ongoing maintenance and the importance of not removing the lock or tag.
Failure to implement LOTO procedures can result in devastating consequences, highlighting the urgency of comprehensive training for all involved personnel.
3. The Significance of Comprehensive Operator Training
While machine guarding and LOTO procedures are essential for preventing accidents, their effectiveness depends on the awareness and competence of operators and maintenance personnel. Comprehensive operator training is the glue of a safe manufacturing environment.
A study conducted by the National Institute for Occupational Safety and Health (NIOSH) found that well-trained operators were significantly less likely to be involved in machine-related accidents.****
Training programs should cover:
- Machine Operation: Operators must have a deep understanding of the machines they work with, including their functions, limitations, and potential hazards.
- Safety Protocols: Training should include proper machine start-up and shutdown procedures and emergency response protocols.
- Identifying Hazards: Operators should be trained to recognize potential hazards and know how to address them safely.
- Communication: Effective communication between operators, maintenance personnel, and supervisors is vital to ensure everyone is on the same page regarding safety procedures and equipment status.
The manufacturing industry forms the backbone of modern society, but its complexities come with a price—worker safety must be an uncompromised priority. Proper machine safety protocols, including machine guarding and lockout/tagout procedures, are the foundation upon which a safe manufacturing environment is built. These measures, coupled with comprehensive operator training, empower the workforce to navigate the challenges of manufacturing safely.
As we move forward, let us collectively commit to fostering a culture of safety in manufacturing. It is not just about compliance; it is about safeguarding the lives and well-being of those who dedicate themselves to the production of the products we rely on daily.
If you are involved in the manufacturing industry, take a moment to visit YellowBird to see how we can assist you in a mock OSHA inspection, training and other resources we offer. Lives and livelihoods depend on it. Together, we can make manufacturing safer for everyone involved.
Sources:
* https://www.bls.gov/opub/mlr/cwc/work-related-injuries-illnesses-and-fatalities-in-manufacturing-and-construction.pdf
** https://www.osha.gov/top10citedstandards
*** https://www.osha.gov/green-jobs/solar/lockout-tagout#:~:text=Approximately%203%20million%20workers%20service,and%2050%2C000%20injuries%20each%20year
**** https://www.ncbi.nlm.nih.gov/pmc/articles/PMC4711279/