How General Industry Can Improve Fall Protection Overnight
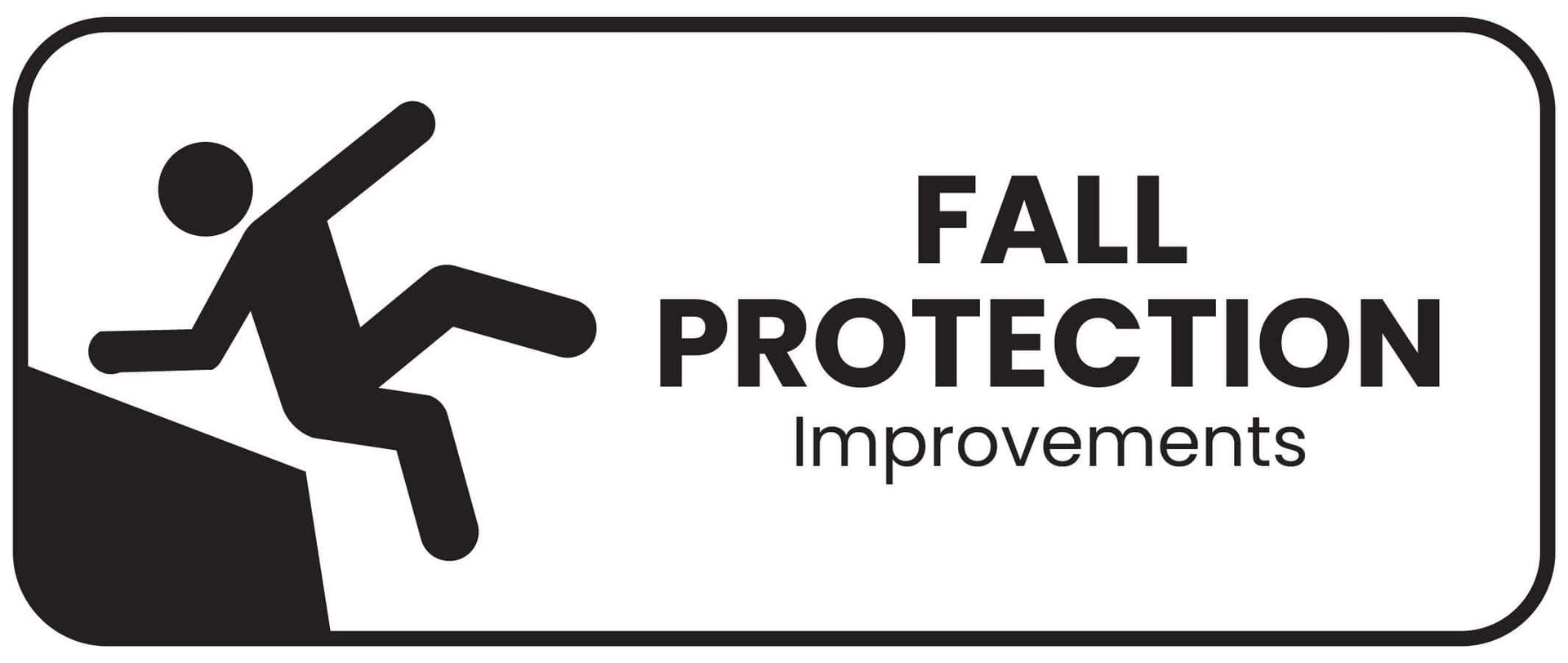
How General Industry Can Improve Fall Protection Overnight
Falls continue to present a constant danger to general industry workers. According to the National Safety Council
, more than 800 workers were killed in 2020 from falls in the workplace, and another 211,640 suffered injuries that were substantial enough to require time off from work. To help reduce these numbers, it’s incumbent upon every employer to provide its employees with the knowledge, tools, and resources needed to properly navigate situations in which fall hazards are present.
It’s virtually impossible to control every aspect of a work environment, and when it comes to fall protection, occasional incidents or near misses are bound to happen. With that said, there are several simple ways general industry leaders can improve their existing fall protection practices to ensure greater safety for every worker at their job sites.
Better Fall Protection Is the Best Business Move
Improving fall protection for workers is a smart business decision for a variety of reasons. Aside from mitigating the risk of death or injury to your employees, investing in enhanced fall protection equipment and education can also lead to fewer workers’ compensation claims across all job sites. In addition, robust fall protection standards will help increase worker retention rates by facilitating a safe and secure work environment for all employees. Read on to learn about several effective fall protection solutions you can enact today, many of which are relatively simple to set up without requiring much time, money, or effort.
Educate Employees
Like all safety standards, fall protection regulations and best practices are subject to frequent changes, making it challenging for workers to access up-to-date information. Although most general industry workers will receive fall protection training at least once a year, any number of alterations to Occupational Safety and Health Administration (OSHA) safety standards or state laws can quickly make any safety training manual or fall protection protocol obsolete.
To avoid this problem, it’s essential to update employee safety education materials the moment any changes are made to existing workplace safety standards. Doing this will ensure that the entire company follows the same guidelines and best practices when working on a job site where fall hazards are present.
Operate With New Equipment
Fall protection equipment will eventually deteriorate from the wear and tear of daily use. Even the most advanced piece of safety equipment can be rendered relatively useless, or even dangerous, after several months in the field.
To keep workers safe, general industry leaders should take steps to ensure all fall protection equipment is carefully inspected and maintained before use. In addition, any damaged or outdated equipment should be rapidly taken out of commission and replaced whenever necessary. Three main types of equipment are used to protect workers from fall hazards.
Safety Nets
After installation, a safety net should be drop-tested to verify its efficacy on the job site. As per OSHA recommendations, you should drop a 400-pound bag of sand onto the net from the highest point where workers could potentially fall. Any debris or objects that fall into the net during the workday should be removed as soon as possible. In addition, it’s vital to inspect safety nets regularly, replacing them as needed whenever someone discovers damage.
Guardrails
Another way to protect workers from falls is by installing guardrails at any location where it’s possible to fall six feet or more. To meet compliance standards, guardrails must be strong enough to sustain 200 pounds of force. If a weak point is found, it’s essential to fix the issue before work proceeds
Personal Fall Arrest Systems
Personal fall arrest systems are the third way to keep workers safe from fall hazards. This type of fall protection equipment consists of a body harness, an anchorage point, and connecting components like lanyards or snap hooks.
It’s critical to inspect all anchorages, connections, and harnesses before use, replacing any component that appears damaged. If a harness is ever subjected to the strain of arresting a fall, the harness must be removed from service immediately and replaced with new equipment.
Limit Control Zones
In some cases, using a guardrail or the most advanced safety equipment isn’t always practical or possible. In these cases, creating a controlled access zone may be necessary to keep unauthorized personnel away from the area.
Be sure to label all control zones, following up-to-date compliance regulations carefully. With that said, it’s best to cap the number of control zones in a given work area as much as possible to minimize the number of fall hazards on the job site.
Want to Prevent the Next Fall? Start Now — With YellowBird.
Falls can happen fast. Preparation must be faster. Whether you’re managing a manufacturing floor , a warehouse , or an industrial facility, you don’t have time for guesswork when it comes to fall protection. With YellowBird, you can act today — not after the next incident.
YellowBird connects you with certified safety professionals who specialize in fall protection for your industry. From on-site equipment inspections to training refreshers and gap analysis, we’ve got your team covered — literally and figuratively.
Worried about outdated harnesses? Missing guardrails? Incomplete training logs? YellowBird Pos can identify high-risk areas and bring your fall protection program in line with OSHA standards — fast. We can be on-site in hours, not weeks. Because worker safety can’t wait for next quarter’s budget.