Do You Understand Lockout Tagout?
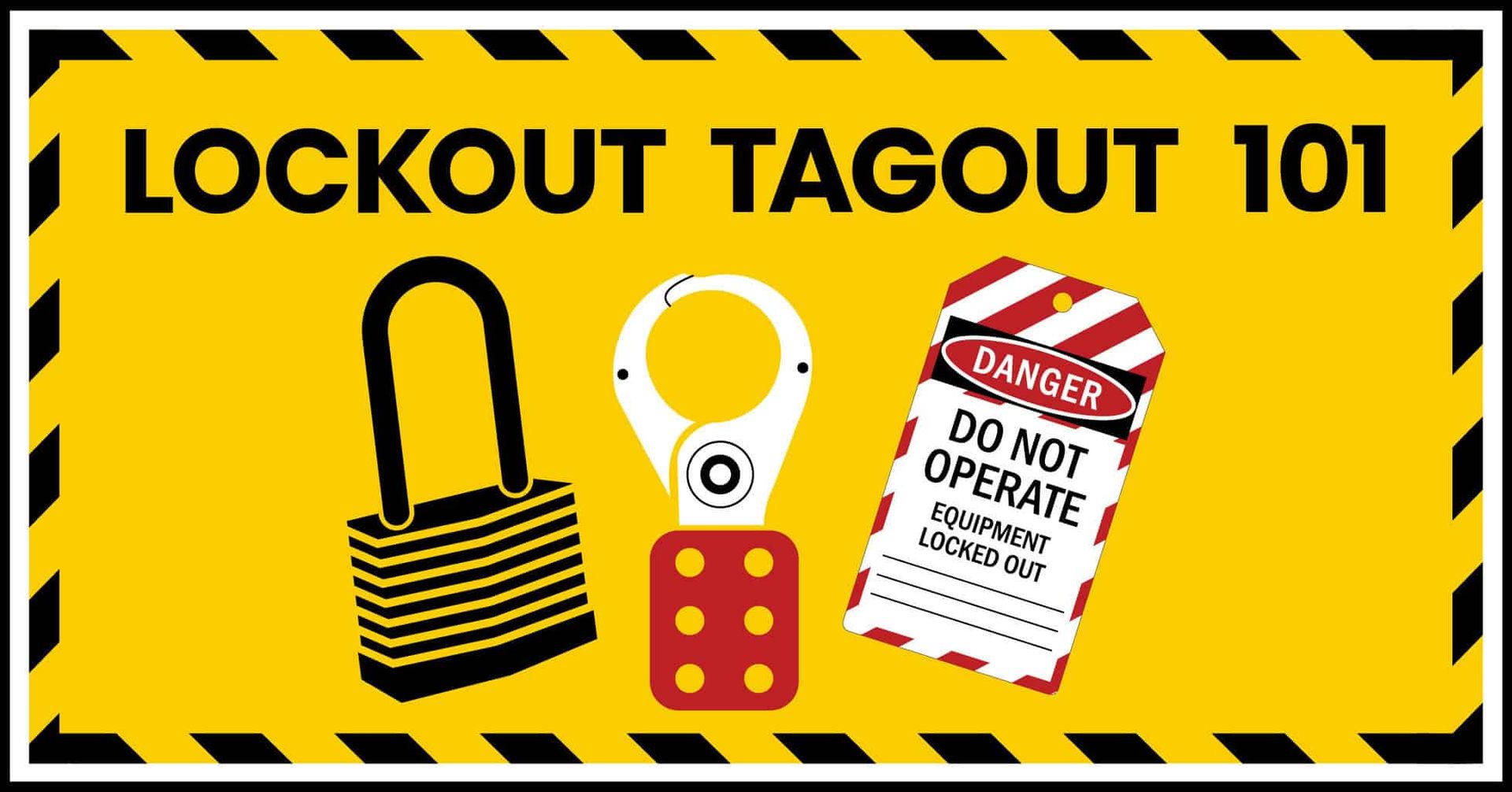
Do You Understand Lockout Tagout?
Unfortunately, preventable injuries in workplaces across the U.S. remain a very real reality. According to data compiled by the National Safety Council
, over 5,000 fatalities occurred in 2019 due to accidents on the job.
To prevent injuries or death in the workplace, companies large and small must take active measures to educate their workers on the potential hazards associated with their jobs. This education should include comprehensive procedures for servicing machines or equipment that pose a risk to employees.
Heavy machinery and industrial equipment can be extremely dangerous, especially when maintenance is needed. To help prevent workplace injuries, OSHA established a series of procedural standards for dealing with various forms of hazardous energy like electrical, thermal, and hydraulic — these safety procedures are known as lockout tagout (LOTO).
Lockout devices effectively prevent equipment or energy sources from activating on accident. Tagout refers to placing a tag on a particular machine, switch, or breaker that advises against activation while the tag remains in place.
Among other things, lockout tagout safety standards ensure machinery remains inactive during installation and maintenance work. The overarching goal of LOTO safety standards is to reduce the number of workplace injuries caused by energized equipment or machines. By following a comprehensive lockout tagout routine, employers can ensure the safety of workers and avoid many costly compliance oversights.
How to Protect Workers
The lockout tagout approach to managing hazardous energy is essential to keeping workers safe. LOTO applies to a range of industries such as general industry, maritime, construction, manufacturing, oil and gas drilling, agriculture, and more. For each industry, OSHA has established a specific set of standards that outline the implementation of lockout tagout safety precautions.
Many of the most commonly reported workplace violations stem from neglecting to follow lockout tagout procedures as defined by OSHA. The purpose of implementing these safety measures is to ensure individuals in the workplace remain protected from hazardous or potentially deadly releases of energy from mechanical faults, hydraulic pressure, electrocution, radiation, and gravity. When employers work to establish a lockout tagout procedure, they are actively contributing to improving the safety of their employees and other individuals who work in or around hazardous energy sources.
The Need to Develop a Lockout Tagout Program
It’s critical for lockout tagout programs to exist for employees to safely work on equipment and machines that break down, malfunction, or require routine maintenance. Lockout tagout procedures should be specific to the hazardous energy being controlled and the type of machine or equipment that needs servicing. Regardless of industry or application, a lockout tagout program should consist of these four main points:
1. Identify potentially hazardous energy sources
This step involves successfully identifying one or more energy sources connected to a machine or piece of equipment that could pose a safety hazard. Even after disconnecting equipment or machinery from a power source, it’s still possible for stored energy in batteries and capacitors to accidentally discharge during maintenance. Likewise, residual energy stored in pneumatic systems or gas lines can be hazardous to workers until the energy is released.
2. Disconnect equipment from all potentially hazardous energy sources
After identifying how energy reaches a machine or device, the next step is to disconnect the equipment in question from any energy sources. LOTO does not apply to self-contained machines or equipment that can easily be de-energized simply by unplugging it from an electrical outlet. If the machine can still retain potential energy after disconnection from its primary source of power, workers should take steps to release that energy in a safe and controlled manner.
3. Install lockout or tagout devices that prevent equipment from energizing
Once the power is disconnected, locks are then attached to stop the system from potentially reactivating. Alternatively, tagout devices are simply descriptive tags of information attached to hazardous equipment that warns against operation until repair work is complete and the tag is removed. It’s important to note that tagout devices do not physically prevent individuals from energizing a machine and do not serve as effective alternatives to energy isolating lockout devices.
4. Verify that the machine or equipment is now safe
At this point, workers should take the time to double-check that the tool or machine is safe to service. Only qualified workers should perform this verification. Following maintenance work on the affected equipment or machinery, a follow-up inspection ensures the work area is clear of workers and items in the area that could impede workplace safety. Only after all these steps are complete can the appropriate personnel remove the lockout or tagout devices.
Company leaders are responsible for developing a practical, safe, and consistent lockout tagout program that successfully addresses the dangers of potentially hazardous energies. Employers who lack a LOTO system risk committing various safety violations, resulting in hefty fines, work disruptions, disciplinary actions, and even employee harm. With a well-rounded, holistic lockout tagout procedure in place, it’s possible to drastically reduce the chances of injuries and fatalities in the workplace.
How to Develop a Lockout Tagout Program
A company’s lockout tagout procedure should be put into written format and openly displayed in the workplace. All workers affected by the LOTO program should receive education on properly implementing lockout tagout safety measures for all relevant systems, machines, and equipment. In general, your lockout tagout program should consist of these basic steps:
1. Determine which LOTO procedure to follow
Locate the appropriate lockout tagout protocols for the machine or device that needs servicing. This procedure should clearly outline how to disconnect the equipment, safely release any energy remaining within the system, and turn the machine back on once the work is complete.
2. Ensure all relevant parties are aware of the lockout tagout
The next procedural step involves ensuring all individuals potentially affected by LOTO receive adequate notice before any work is started. This notice should include where the work is taking place, who is involved, and how long machinery, equipment, or devices will remain offline. The appropriate personnel should make updates to any notifications whenever plans change.
3. Identify potentially hazardous sources of energy
The next step of any lockout tagout procedure is to record any potentially hazardous energy sources related to the equipment or machine — and document what actions need to take place to expel this possible risk. Be aware that in some cases, simply unplugging equipment from its primary power source does not guarantee that the system is safe. For instance, a machine powered by steam or gas can still retain pressure even after it’s deactivated.
4. Disable machinery to be serviced
Closely follow the procedure outlined in your company’s LOTO literature to safely shut down the machine or equipment. This literature should provide a comprehensive, step-by-step process for powering down the specific piece of equipment requiring maintenance. When equipment is upgraded or replaced, it’s critical to modify this information to reflect any changes.
5. Attach tags or lockout devices to the equipment
Each worker is responsible for keeping up with their personal energy-isolating locks and tags. Lockout devices physically prevent machinery or equipment from becoming energized while tags serve as a deterrent against powering on the equipment.
6. Purge any residual potential energy in the machine
As mentioned, even after the equipment is unplugged or deactivated, energy can remain within the system. During this step, the proper individual(s) should take the time to ensure the affected area is clear of personnel and obstructions. Then the disabled machinery or equipment should be tested in an effort to release any stored active energy.
7. Verify the machine is completely deactivated
Double-check that the locked-out machine is safe by trying to turn it on. If all procedures are followed correctly, the machine should remain offline and entirely unresponsive to controls. To further improve safety, never test equipment when others are nearby.
8. Verify that controls are not in the on position
This is a very important step that workers can easily overlook. Make sure all controls to the equipment or machine in question remain in the off position for the duration of the work. Following this step ensures workers are not injured when the connection to an energy source is reestablished.
The Takeaway : Injuries That Happen Without LOTO Could Have Been Prevented
Still think your workplace doesn’t need a Lockout Tagout program? Think again. The cost isn’t just compliance violations—it’s lives. One mistake. One oversight. That’s all it takes to change someone’s life forever—or end it.
You already know what LOTO is. Now the real question is—Do your teams actually use it the right way? Every time?
At YellowBird, we connect you with vetted, experienced LOTO professionals who’ve seen the worst—and know how to prevent it. Don’t leave safety to chance or checklists. Build a program that sticks. Train people who remember. And sleep better knowing you did your job to protect your team.
Stop playing the odds. Start your Lockout Tagout program the right way. Get matched with a certified LOTO expert from YellowBird today!